The Relationship between the Hot Tack of Packaging Material and Filling Efficiency
Source:
Viewer:2694
Issuing Date:2008-10-30
Click to download!
Abstract:This paper introduces the difference and relationship between the hot tack and ultimate strength. It uses example to introduce the close relationship between hot tack and choices of filling product line.
Keywords:
hot tack
, packaging
, filling efficiency
The hot sealing performance of packaging materials is the main parameter to assess packaging ability of materials. It includes the hot tack and ultimate strength. Hot tack has been used to check the strength to peel off hot sealing parts, when shortly after hot sealing (not cold yet). Ultimate strength has been used to check the strength to peel off the hot sealing parts, when the parts have already gone cold. These parameters vary hugely with one material. However, the proper application of these parameters usually affects the choices of packaging materials and the actual filling efficiency. This paper is going to introduce the application of hot tack of materials by using filling product line material as an example.
1 The Application of Hot Tack
Today, in food, medicine, cosmetics, and other areas, soft packaging often uses Form-Fill-Seal Machine. In these filling production lines, soft package manufacture is carried out at the same time with filling. The filling method is basically to fill the product into the package from a certain height. The falling cast strong impact to the bottom of packages. If the bottom cannot bear the impact, the bottom will crack—package break. It will affect the cleanness and the filling efficiency. As on the filling product line, the time between hot sealing manufacture of package and product filling is very little, it is almost impossible to cold down the hot sealing parts in such a short time period. It can be seen that the ultimate strength is not applicable in this case. The hot tack should be adopted. It is commonly recognized that optimization of hot sealing process is an efficient way to shorten the packaging time. The hot tack test will be helpful for manufacturers to choose the best hot sealing parameters.
Thus, the difference between hot tack and ultimate strength is clear. Hot tack is applied to assure the running of filling product line. The hot tack will affect the filling efficiency and package break rate directly. The hot sealing performance is usually used to indicate the containment ability of materials. It is to assure that the hot sealed parts are not going to leak during transportation, storage and exhibition. It is the pre-condition to realize the functions of packaging materials.
2 Case Studies
How to choose the best hot seal parameters of product line by making use of hot tack testing? The relationship between hot tack and hot sealing parameters of product line is going to be introduced in the following paragraph. It is the case of Labthink helping its clients to test product.
The client is an East Asian food production company. The company wanted to make a choice between A and B film, which share similar performance parameters. The company wanted a film to satisfy the requirement of product line and make the product line more efficient. The hot sealing side of material, the hot sealing time and pressure are all fixed. Client required that the hot sealing temperature to be no more than 133℃ and the hot tack to be no lower than 2N. Given the conditions above, the hot sealing time should be as short as possible and energy saving.
1 The Application of Hot Tack
Today, in food, medicine, cosmetics, and other areas, soft packaging often uses Form-Fill-Seal Machine. In these filling production lines, soft package manufacture is carried out at the same time with filling. The filling method is basically to fill the product into the package from a certain height. The falling cast strong impact to the bottom of packages. If the bottom cannot bear the impact, the bottom will crack—package break. It will affect the cleanness and the filling efficiency. As on the filling product line, the time between hot sealing manufacture of package and product filling is very little, it is almost impossible to cold down the hot sealing parts in such a short time period. It can be seen that the ultimate strength is not applicable in this case. The hot tack should be adopted. It is commonly recognized that optimization of hot sealing process is an efficient way to shorten the packaging time. The hot tack test will be helpful for manufacturers to choose the best hot sealing parameters.
Thus, the difference between hot tack and ultimate strength is clear. Hot tack is applied to assure the running of filling product line. The hot tack will affect the filling efficiency and package break rate directly. The hot sealing performance is usually used to indicate the containment ability of materials. It is to assure that the hot sealed parts are not going to leak during transportation, storage and exhibition. It is the pre-condition to realize the functions of packaging materials.
2 Case Studies
How to choose the best hot seal parameters of product line by making use of hot tack testing? The relationship between hot tack and hot sealing parameters of product line is going to be introduced in the following paragraph. It is the case of Labthink helping its clients to test product.
The client is an East Asian food production company. The company wanted to make a choice between A and B film, which share similar performance parameters. The company wanted a film to satisfy the requirement of product line and make the product line more efficient. The hot sealing side of material, the hot sealing time and pressure are all fixed. Client required that the hot sealing temperature to be no more than 133℃ and the hot tack to be no lower than 2N. Given the conditions above, the hot sealing time should be as short as possible and energy saving.
We used Labthink HTT-L1 hot adhesive pull tester to test the hot adhesive of A, B two types of films. Hot sealing time was set to 0.3s, 0.5s, 0.7s; sealing temperature was set to 115 ℃, 118 ℃, 121 ℃, 124 ℃, 127 ℃, 130 ℃, 133 ℃. Other parameters were set in accordance with customer requirements. The width of the test sample was 25mm as customer required. Figure 1 and 2 is the test data curve.
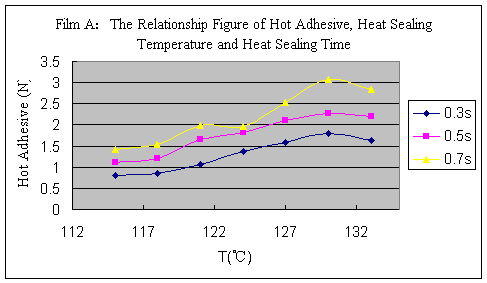
Figure 1. Film A:The Relationship Figure of Hot Adhesive, Heat Sealing Temperature and Heat Sealing Time
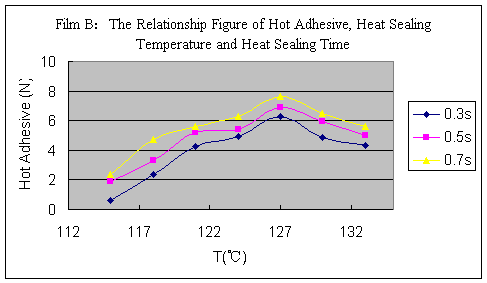
Figure 2. Film B:The Relationship Figure of Hot Adhesive, Heat Sealing Temperature and Heat Sealing Time
In fact, there is a best temperature point in order to achieve the best hot adhesive of film materials. When the hot sealing temperature rises above the best temperature point, the hot adhesive will drop under the best point. From the figure 1 and 2 we can see that the best hot sealing temperature is about 130 ℃, while B's best sealing temperature is about 127 ℃.
Based on data of film A, when the hot sealing time is 0.3s, the hot adhesive did not reach the requirement of client; when the hot sealing time is 0.5s, sealing temperature at 127 ℃ ~ 133 ℃, the material could just reach the requirement of client; but when the hot sealing time is 0.7s and the temperature is between 127 ℃ ~ 133 ℃, the hot adhesive of the material could well satisfy the requirement. Thus in the case of film A, hot sealing time of more than 0.5s and temperature of 127 ℃ ~ 133 ℃ can satisfy the need of clients. But to film B, in the same condition of film A, film B showed better hot adhesive than film A. when the hot sealing time is no less than 0.3s and the temperature is more than 118 ℃ ~ 133 ℃, film B can satisfy customer’s need for hot adhesive. As the time of hot sealing increased, the time need for hot sealing showed a significant drop. When the not sealing time reached 0.7s and temperature between 115 ℃ ~ 133 ℃, film B could be very satisfactory.
Referring to the above test data, we believe that the film should be B, and the production line sealing parameters can be set: sealing time of 0.3 s ~ 0.5s, sealing temperature of 118 ℃. Of course, sealing temperature should also be further tested to determine the best value. It should be noticed that there values should be somehow over the margin in order to avoid uneven sealing, which could be caused by mechanical or material problem. Simply from the point of view of materials, we believe film A would lower the efficiency of filling and raise the energy cost of product line. However further analysis should be base on some other issues like material cost and the best efficiency of the who product line.
3 Summaries
In order to reasonably set the hot sealing parameters of filling product lines, hot tack should be the main concern. By using hot adhesive pull tester, we can adjust the hot sealing time, hot adhesive time, hot sealing temperature and hot sealing pressure according to our will. Taking the actual situation of product line into consideration, we can figure out the best parameters combination from the test data chart. Of course, the cost of materials should also be considered. As a result the production cost and efficiency will both be optimized.
Based on data of film A, when the hot sealing time is 0.3s, the hot adhesive did not reach the requirement of client; when the hot sealing time is 0.5s, sealing temperature at 127 ℃ ~ 133 ℃, the material could just reach the requirement of client; but when the hot sealing time is 0.7s and the temperature is between 127 ℃ ~ 133 ℃, the hot adhesive of the material could well satisfy the requirement. Thus in the case of film A, hot sealing time of more than 0.5s and temperature of 127 ℃ ~ 133 ℃ can satisfy the need of clients. But to film B, in the same condition of film A, film B showed better hot adhesive than film A. when the hot sealing time is no less than 0.3s and the temperature is more than 118 ℃ ~ 133 ℃, film B can satisfy customer’s need for hot adhesive. As the time of hot sealing increased, the time need for hot sealing showed a significant drop. When the not sealing time reached 0.7s and temperature between 115 ℃ ~ 133 ℃, film B could be very satisfactory.
Referring to the above test data, we believe that the film should be B, and the production line sealing parameters can be set: sealing time of 0.3 s ~ 0.5s, sealing temperature of 118 ℃. Of course, sealing temperature should also be further tested to determine the best value. It should be noticed that there values should be somehow over the margin in order to avoid uneven sealing, which could be caused by mechanical or material problem. Simply from the point of view of materials, we believe film A would lower the efficiency of filling and raise the energy cost of product line. However further analysis should be base on some other issues like material cost and the best efficiency of the who product line.
3 Summaries
In order to reasonably set the hot sealing parameters of filling product lines, hot tack should be the main concern. By using hot adhesive pull tester, we can adjust the hot sealing time, hot adhesive time, hot sealing temperature and hot sealing pressure according to our will. Taking the actual situation of product line into consideration, we can figure out the best parameters combination from the test data chart. Of course, the cost of materials should also be considered. As a result the production cost and efficiency will both be optimized.
Title:The Relationship between the Hot Tack of Packaging Material and Filling Efficiency
Link:http://service.labthink.cn/en/article-Routine-info-110118135.html
Labthink Copyrights. Please do not copy without permission! Please indicate source when copy.
Link:http://service.labthink.cn/en/article-Routine-info-110118135.html
Labthink Copyrights. Please do not copy without permission! Please indicate source when copy.
Member Registration and Login In
If you are already a member of us, please login in! | If you are not a member of us, please register for free! | ||
![]() ·Forget password? |
|
![]() ·Terms and Conditions If you have questions, please phone 86-531-85811021 |